See you at HOST Milan 2023!
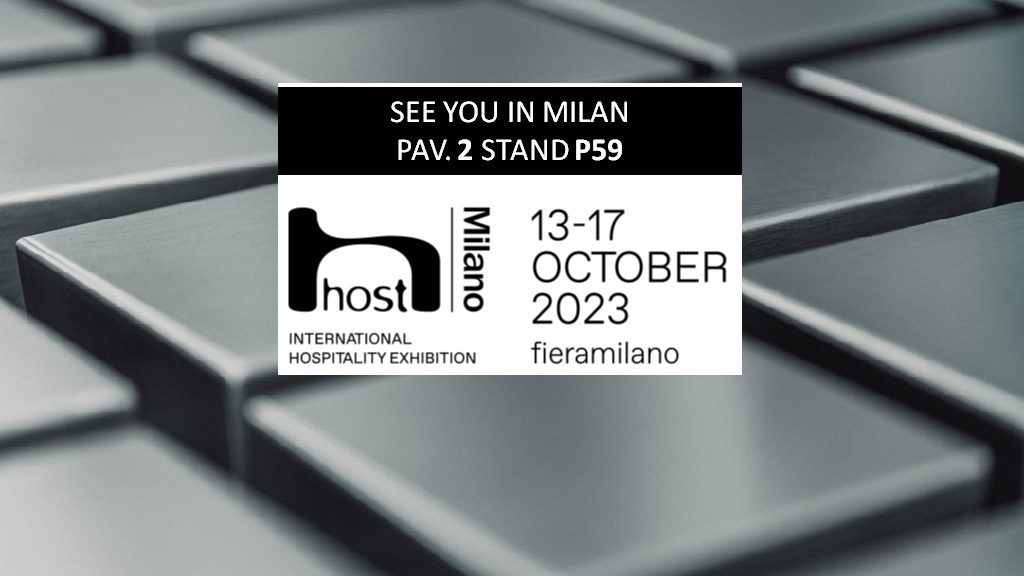
Siamo entusiasti di annunciare la nostra partecipazione anche quest’anno alla prestigiosa fiera Host di Milano, un evento imperdibile nel mondo dell’ospitalità e della ristorazione.La fiera rappresenta per noi un’importante opportunità per condividere le nostre più recenti innovazioni in termini di tecnologie e processi, nonché per incontrare i nostri clienti e partner.Vi aspettiamo al Padiglione 2, […]
Stainless steel: sustainability and eco-friendliness
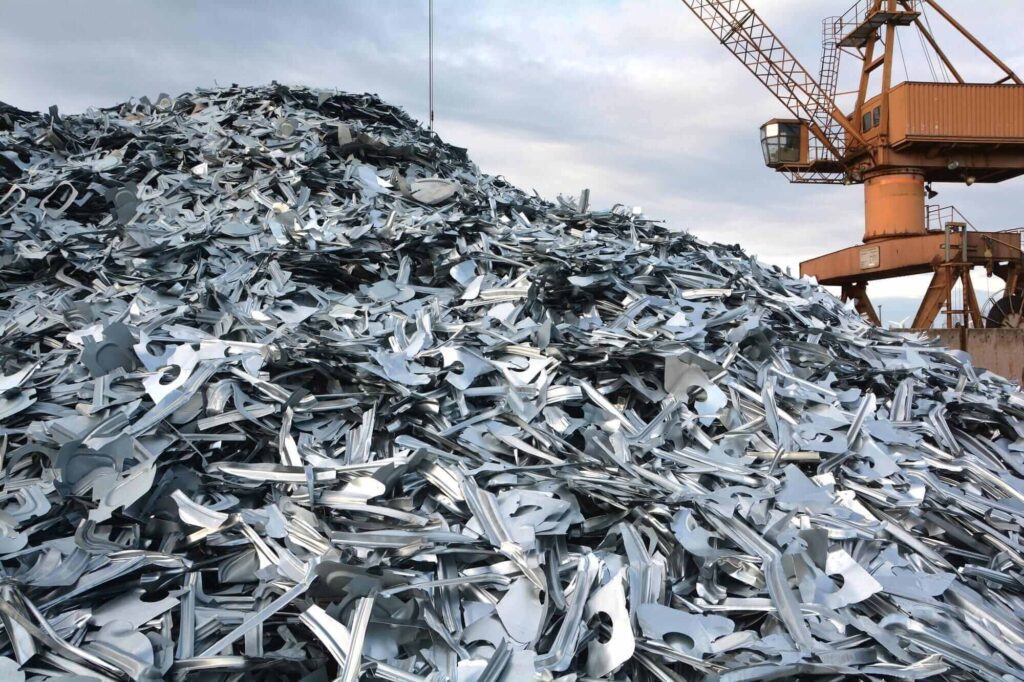
L’acciaio inox è un materiale sostenibile dalle importanti caratteristiche che si può utilizzare in diversi settori e applicazioni. Inventato nel XIX secolo dal tecnico metallurgico britannico Harry Brearley, l’acciaio inossidabile è composto principalmente da ferro, carbonio e cromo, che possono essere abbinati ad altre leghe per aumentarne la resistenza e per ampliarne i possibili usi.. […]
Stainless steel in the food and medical sector: advantages and safety

L’acciaio inox è uno dei materiali maggiormente utilizzati nel settore alimentare e medicale perché offre numerosi vantaggi ed evita il rischio di contaminazioni. Composto soprattutto da ferro e cromo, a cui si abbinano altre leghe in diverse quantità, l’acciaio inossidabile è durevole, resistente alla corrosione, facile da pulire e da mantenere nel tempo. Vediamo meglio […]
Metal’s case history: how we optimised costs without changing the aesthetics and functionality of the product
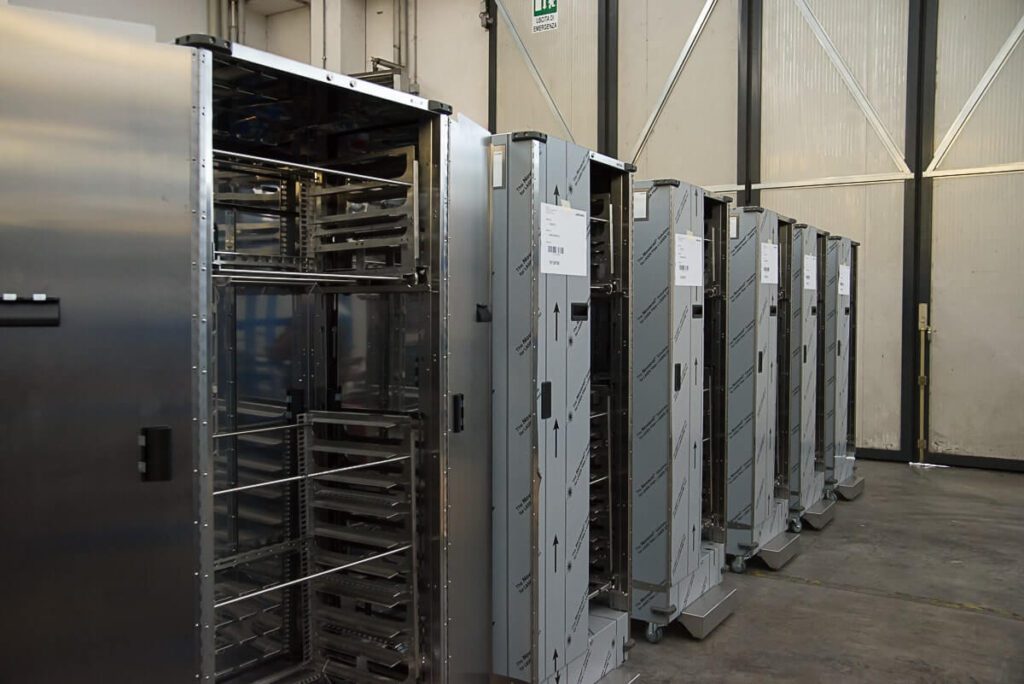
La lavorazione dell’acciaio inox è solo uno dei passaggi del nostro processo produttivo. In Metal’s, infatti, ci impegniamo a fornire un servizio completo ai nostri clienti, che parte dalla consulenza e arriva alla consegna. Ne abbiamo già parlato nell’articolo su come lavoriamo. Ma in che modo viene sviluppato un progetto, concretamente? E come approcciamo una […]
Advanced metal machining: the advantages of laser technology in the metal industry
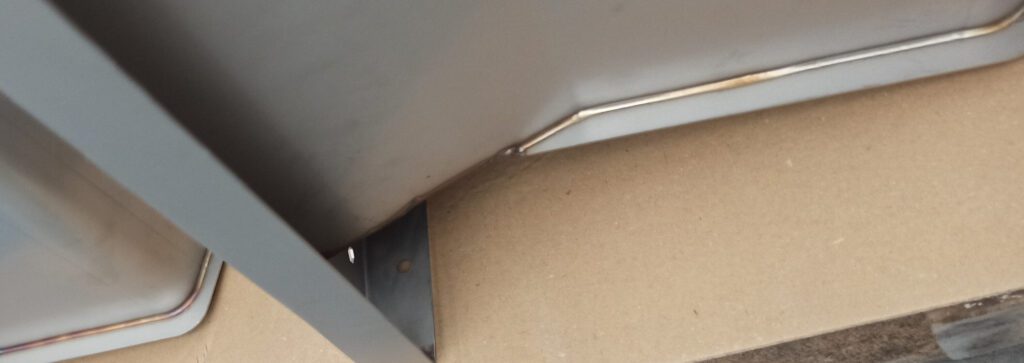
La tecnologia laser per la lavorazione dei metalli è un sistema di lavorazione molto preciso che prevede l’emissione diretta di una sorgente di luce dall’alta densità energetica su un’area specifica del materiale allo scopo di tagliarlo, saldarlo oppure inciderlo con estrema pulizia e velocità. Sviluppata negli anni Sessanta, la tecnologia laser si è perfezionata nel […]
New 6-Days project
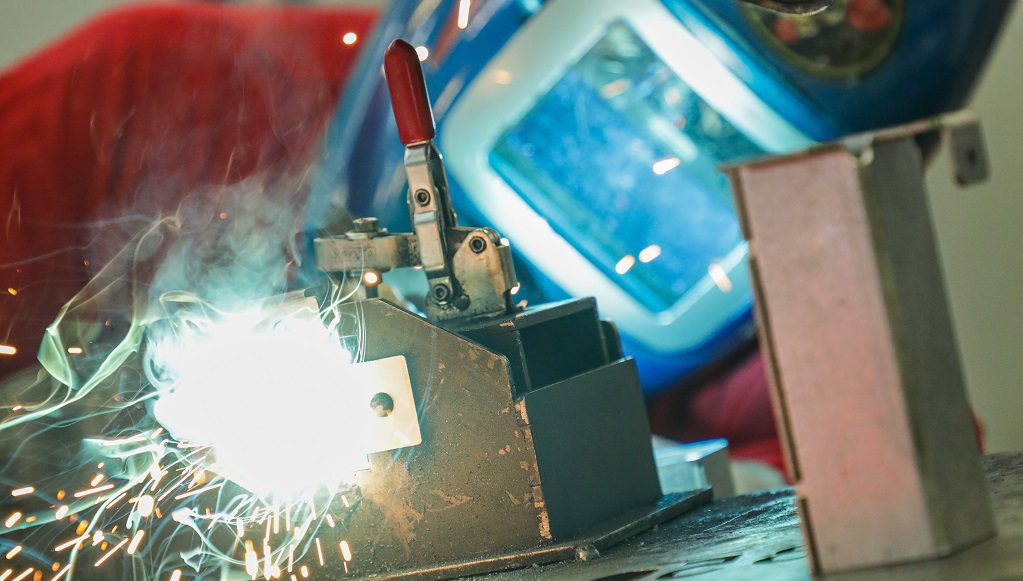
Dopo il buon esito del progetto 6-days avviato lo scorso ottobre abbiamo deciso di ripetere il programma con l’introduzione di 8 nuove figure dal 13/03/23.Il progetto studiato per agevolare i nuovi inserimenti prevede 30 ore settimanali in 6 giorni.Le risorse faranno dapprima una formazione teorica nella Metal’s Academy e poi saranno inserite nei reparti produttivi, […]
We have new welding machines equipped with laser technology
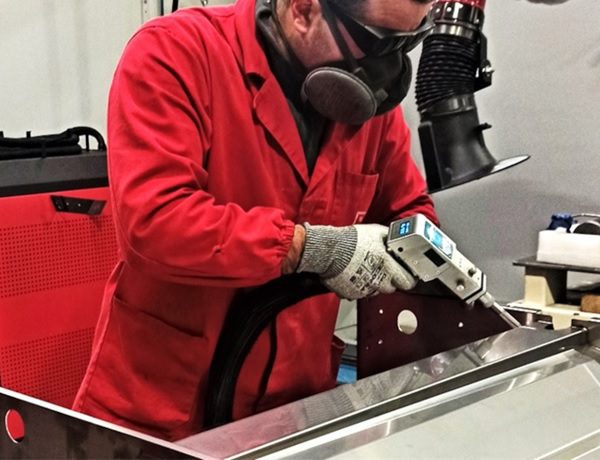
Da qualche mese abbiamo introdotto nei nostri reparti produttivi due nuove saldatrici laser. Si tratta di una tecnologia di saldatura innovativa che ci ha portato una serie di numerosi vantaggi, tra i quali aumento della velocità di esecuzione, migliore risultato estetico e funzionale. A breve verrà sviluppato inoltre un nuovo impianto completamente automatico dotato di […]
Company welfare extended for the year 2023
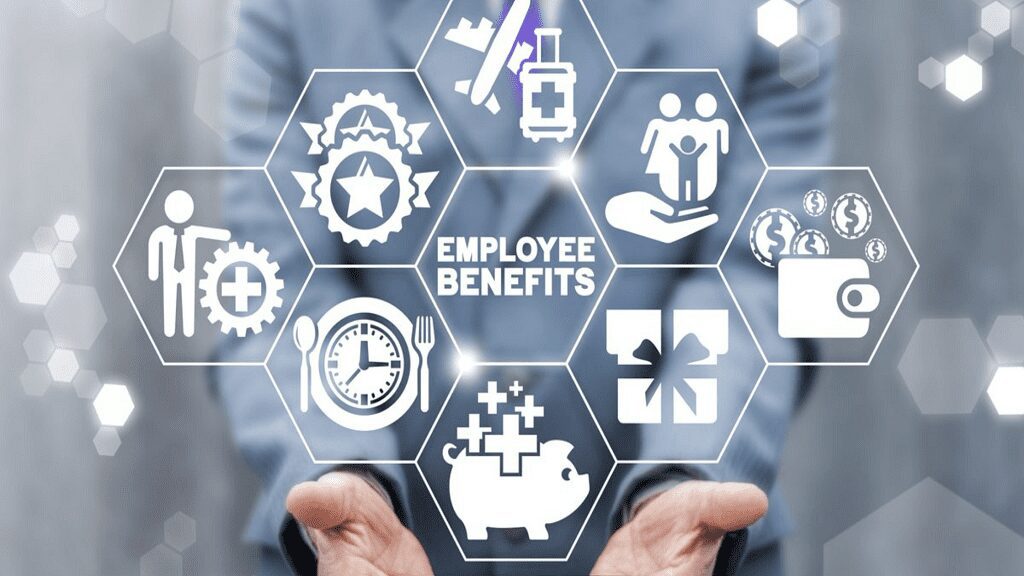
Also for the current year the COMPANY WELFARE system, introduced during 2019, has been reconfirmed.
A useful tool for employees for a better conjugation of family and professional life.
Interesting contributions for children, studies, school results and reimbursements for kindergartens in support of the family, as well as the free loan.
New certification 3834-2
Abbiamo ottenuto con successo dall’ente TÜV SÜD la Certificazione ISO 3834-2. La norma ISO 3834 è dedicata alla saldatura e definisce i requisiti di qualità per la saldatura utili sia per coloro che eseguono queste attività, sia per coloro che valutano le capacità del costruttore di produrre manufatti saldati secondo i requisiti di norma. Essere […]
We have our own generator for self-production of nitrogen
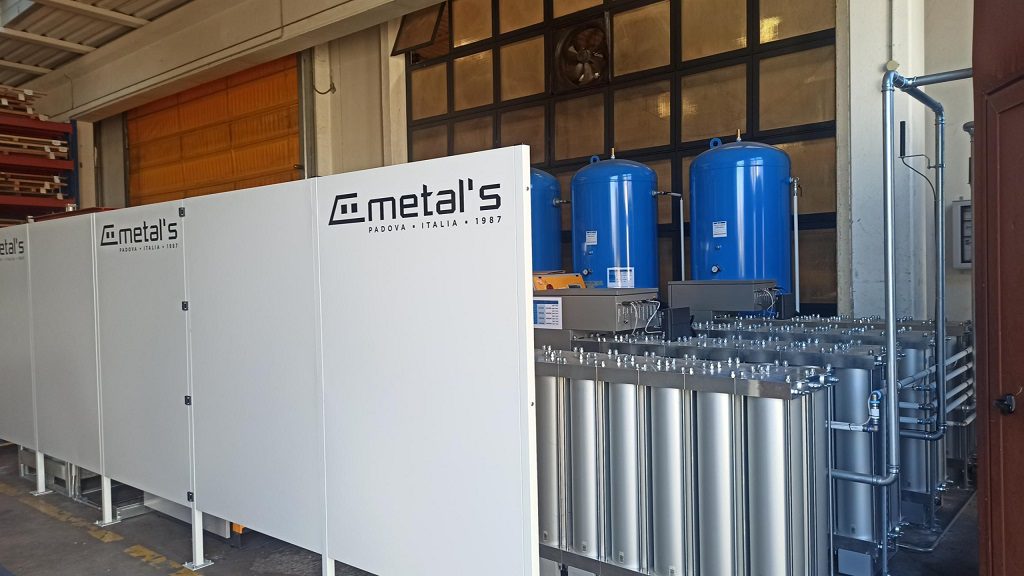
In abbinata con l’ampliamento dell’impianto fotovoltaico e principalmente per avere stabilità dei costi di produzione di gas nel tempo abbiamo avviato da qualche settimana un nuovo impianto per l’autoproduzione di azoto.Avere sempre a disposizione il gas che alimenta i nostri impianti di taglio è per noi di fondamentale importanza e questo impianto oltre a darci […]
We moved to our new offices!
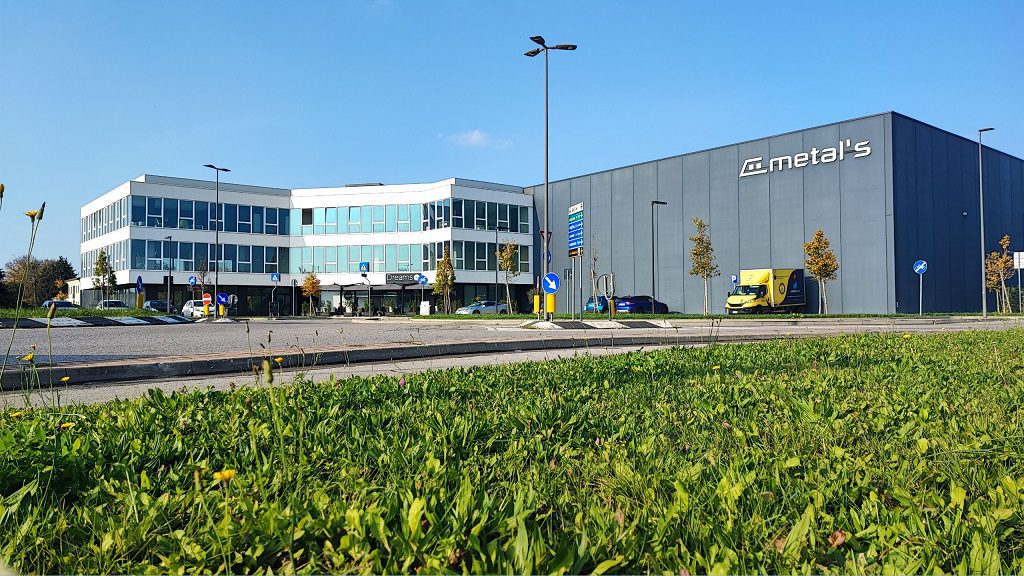
Gli uffici direzionali di Metal’s si sono trasferiti nella nostra nuova palazzina che si trova al lato sud rispetto gli stabilimenti esistenti. I nuovi uffici, tutti in open space, godono di spazi molto ampi e ci hanno permesso di creare un ambiente moderno che favorisce la connessione e la produttività.
Metal’s and the Sicily project
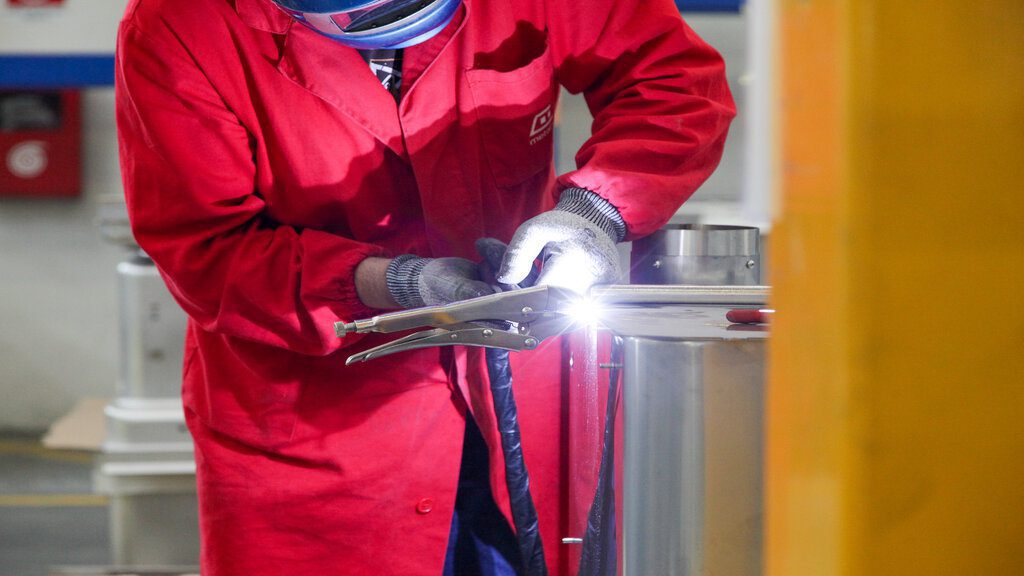
In continuazione al progetto formativo Sicilia, già avviato lo scorso febbraio 2022, con il quale abbiamo introdotto nei mesi una decina di persone nei reparti di saldatura e piegatura, stiamo procedendo in questi giorni con l’inserimento di altre risorse sempre provenienti dalla regione Sicilia. Si tratta di un gruppo di persone che saranno dapprima formate […]
Metal’s Academy has been inaugurated this week!
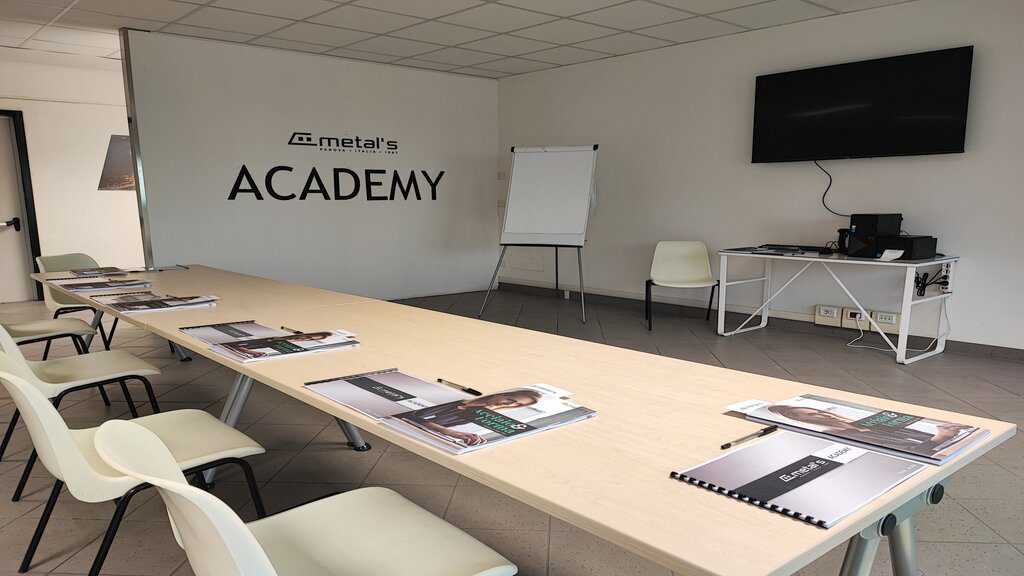
Metal’s Academy è il nuovo percorso formativo pensato per chi vuole entrare a far parte del mondo Metal’s.Il centro darà la possibilità ai nuovi assunti, per determinate mansioni, di fare una formazione completa prima di immergersi nei reparti produttivi.La formazione sia teorica che pratica, sarà focalizzata sulle tecnologie più critiche e complesse presenti in azienda.Auguriamo […]
Have you already seen the second issue of our magazine “Acciaio&Forma”?
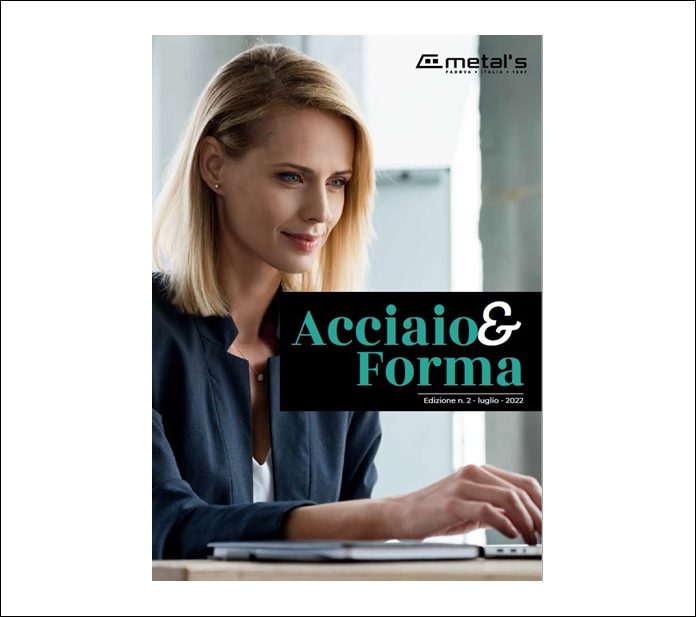
E’ stata pubblicata da poco l’edizione n. 2 della ns. rivista!Tutto ruota attorno al tema principale: Metal’s come fornitore completo nella fornitura di sistemi, macchine e dispositivi sviluppati, prodotti e assemblati secondo i vostri progetti.Grazie alla nostra profonda conoscenza delle materie prime e delle tecnologie implementiamo le tue specifiche nei vari processi produttivi, governando l’intero […]
Metal’s: a single reference for your complex projects
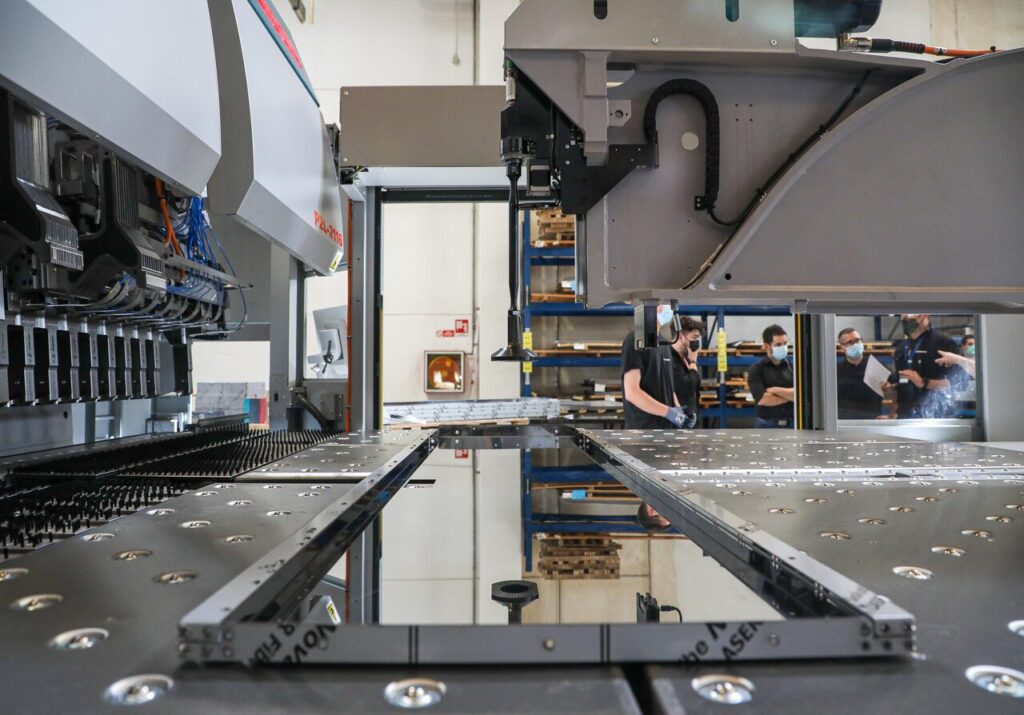
Our goal is to turn your problems into solutions. We check the feasibility of each project, we evaluate it from a technical and economic point of view, and provide you with technically perfect and economically sustainable complex assemblies.
Merry Christmas and Happy New Year!
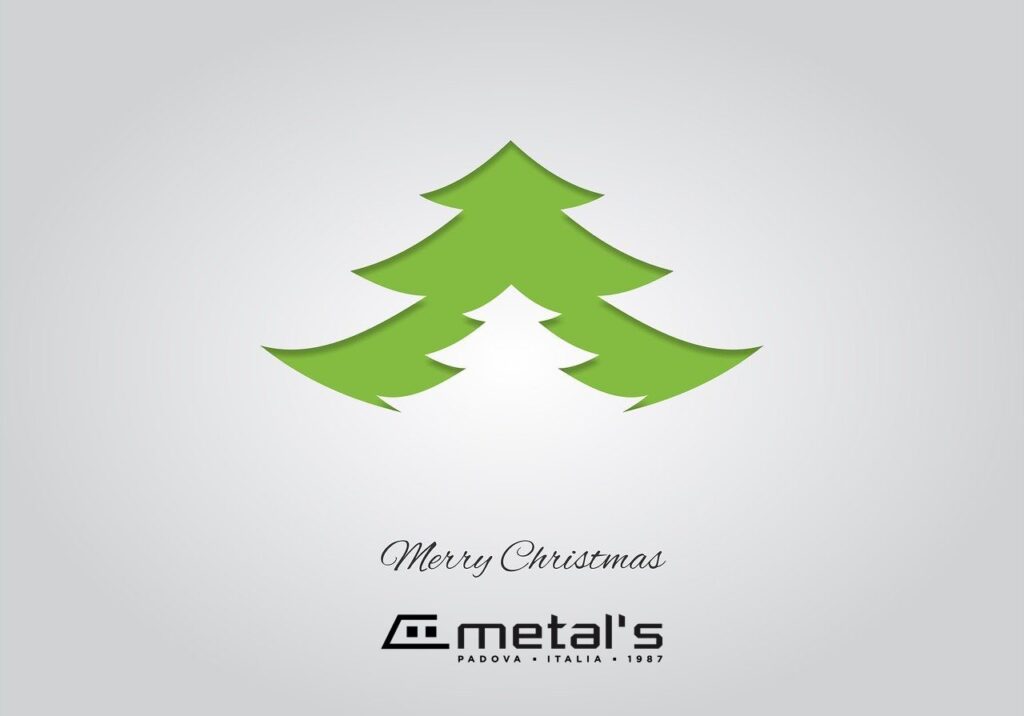
Metal’s wishes you all Merry Christmas and a wonderful New Year. Our offices will be closed from December 24, 2021 until January 2, 2022 due to Christmas holidays.
Project financed with POR FESR 2014-2020 Veneto Region
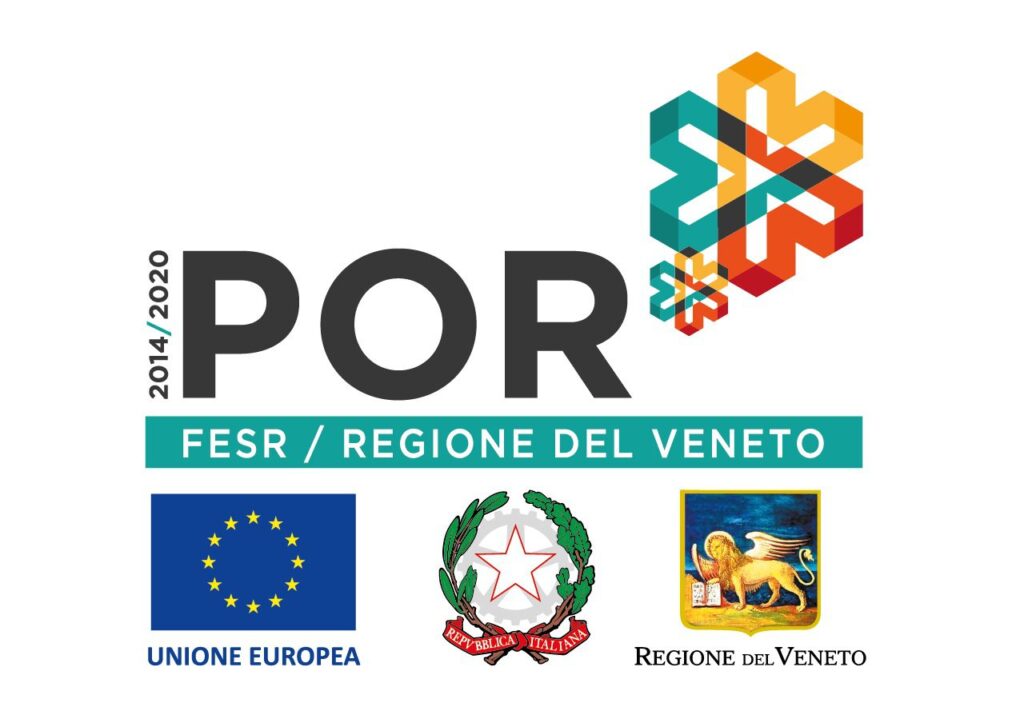
Metal’s è orgogliosa di essere partner del progetto Asse 3 Competitività dei sistemi produttivi.Progetto finanziato tramite il Programma Operativo Regionale (POR) ed i Fondi Europei di Sviluppo Regionale (FESR) 2014-2020 – 3.1.1 sub A Bando per l’erogazione di contributi alle imprese del settore manifatturiero e dell’artigianato di servizi – Sportello A della Regione Veneto.L’intervento che […]
Have you already seen the first issue of our magazine “Acciaio&Forma”?
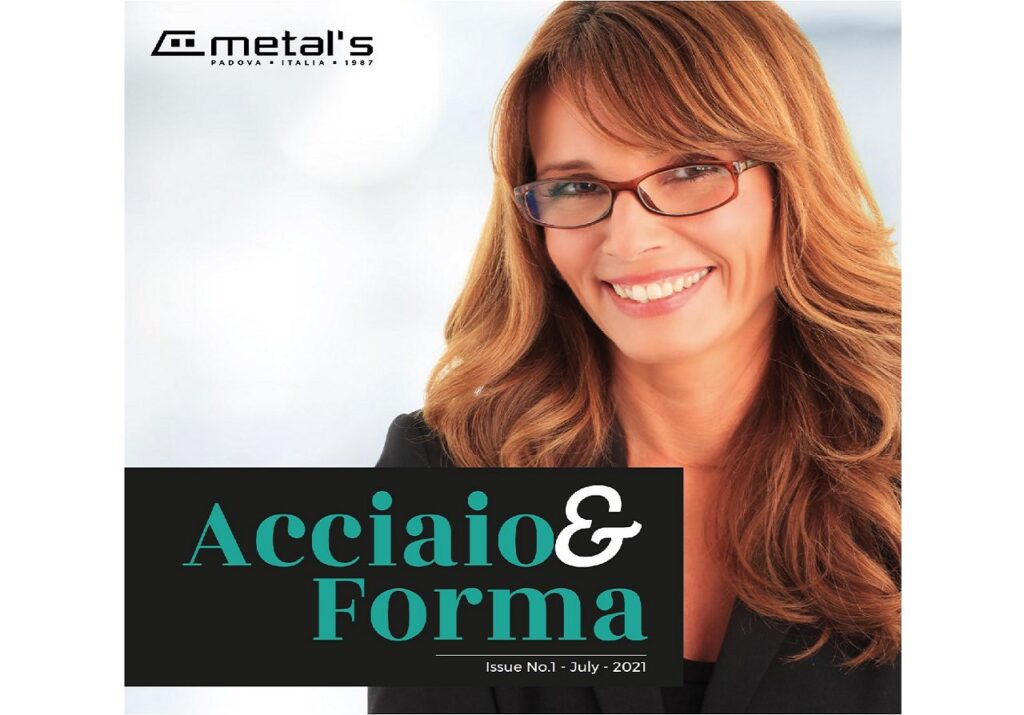
Tutto ruota attorno al tema principale: Metal’s come fornitore completo nella fornitura di sistemi, macchine e dispositivi sviluppati, prodotti e assemblati secondo i vostri progetti. Immergetevi nella lettura scaricando il pdf completo per entrare nel nostro mondo e scoprire i benefici che ne derivano! Buona lettura !