Metal’s case history: technical modifications to improve project performance
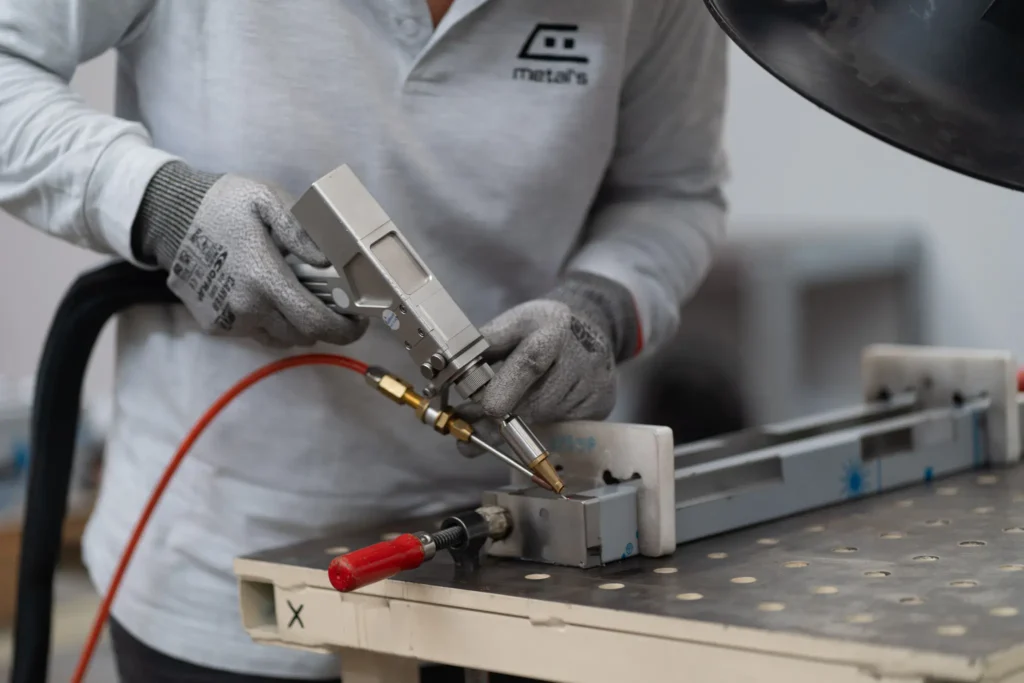
Alcune modifiche tecniche su un progetto già concordato e avviato da tempo possono migliorare la qualità di un assieme o un semilavorato a livello funzionale, estetico e, non da ultimo, economico. Cambiamenti che coincidono spesso con l’arrivo di nuove tecnologie, sempre più all’avanguardia e performanti. Quando il parco macchine di Metal’s si arricchisce di una nuova apparecchiatura funzionale al progetto, il nostro ufficio tecnico valuta eventuali implementazioni al […]