Um die spezifischen Anforderungen unserer Kunden zu erfüllen, können wir bei Metal’s Aufträge mit zertifizierter Schweißtechnik ausführen.
Wir verfügen über einen großen Maschinenpark, mit automatisierten Systemen ausgestattet: dies ermöglich es uns, bestimmte Arbeiten zu zertifizieren, sowie die Produktion zu verbessern und die Abläufe zu beschleunigen, um immer termingerecht zu liefern.
Als alleiniger Ansprechpartner kümmern wir uns sorgfältig um jedes Detail und schlagen Maßnahmen vor, um ein Projekt sowohl in Bezug auf die Produktion als auch auf Kosten und Logistik zu optimieren. Eines unserer Ziele ist es, den gesamten Prozess zu optimieren und jede Phase nachhaltiger zu gestalten, auch im Hinblick auf den Transport.
In dieser Fallstudie möchten wir erläutern, wie wir Ihnen Halb- und Fertigbaugruppen mit Schweißzertifizierung liefern können. Außerdem zeigen wir Ihnen die Vorteile eines vollständig geplanten und organisierten Systems.
Zertifizierte Schweißprodukte und eine sorgfältige Organisation der Logistik: eine Case History von Metal’s
Jedes Projekt wird nach der Bewertung durch unsere Konstruktion umgesetzt, auch wenn es von einer Idee des Auftraggebers ausgeht. Auf diese Weise können wir die Produktionsmachbarkeit prüfen und mögliche Schwierigkeiten erkennen, wobei wir stets eine aktive und kooperative Zusammenarbeit pflegen. Falls erforderlich, schlagen wir Verbesserungen vor, um Kosten zu senken, die Produktionszeiten zu verkürzen oder eine größere Nachhaltigkeit beim Transport zu gewährleisten.
So war es zum Beispiel bei einem wichtigen Kunden aus der Lebensmittelverarbeitungsbranche, der eine zertifizierte Lösung benötigte.
Der Fall und der Vorschlag in Kürze: Notwendigkeit, Spalten zu eliminieren
Ein bekanntes deutsches Unternehmen mit internationalem Vertrieb hat uns die Herstellung eines Ofens mit dichten Schweißnähten und ohne Spalten in drei verschiedenen Größen beauftragt.
Das Ziel? Die Ansammlung von Backrückständen zu vermeiden in schwer zu reinigenden Bereichen (wie z.B. Spalten zwischen zwei Komponenten, Ecken oder kleinen Ritzen, die zur Oxidation des Materials führen) und die Lebensdauer des Produkts zu verlängern.
Unser Vorschlag: gezieltes und zertifiziertes Roboterschweißen
Um die Anforderungen des Käufers zu erfüllen – einschließlich der kontinuierlichen Produktion von etwa 6000 Stück pro Jahr – haben wir einen automatisierten internen Schweißprozess vorgeschlagen.
Es handelt sich um eine präzise Bearbeitung, die sich auf die Funktionsbereiche der Ofenkomponenten konzentriert und es uns ermöglicht hat, die Spalten der Verbindung zu schließen (d.h. die Hohlräume, die zwischen den Teilen entstehen können und in denen sich Schmutz oder Backrückstände ablagern können).
Tests und Prototypen für ein hervorragendes Ergebnis
Bevor die Serienproduktion beginnt, sind wie bei jedem Projekt Tests und Prototypen erforderlich, die am ausgewählten Material durchgeführt werden (in diesem Fall handelte es sich um lebensmittelechten Edelstahl). Dies ermöglicht uns, die Anforderungen des Kunden zu erfüllen, die Bearbeitungen zu perfektionieren, sie zu beschleunigen und Abfälle zu vermeiden.
Für die Herstellung der spaltfreien Öfen hat der Kunde neben einer Reihe von Überprüfungstests – die bei Metal’s durchgeführt wurden – auch selbständig externe Dauerprüfungen in einem spezialisierten Labor durchgeführt. Dies ermöglichte es dem Kunden, die Lebensdauer des Produkts gemäß dem vorgesehenen Einsatz zu simulieren (unter Berücksichtigung von Faktoren wie: Betriebsbedingungen, Sättigungsumgebung, Feuchtigkeit und Salzgehalt).
Der Produktionsstart
Nachdem die Vorprüfungen erfolgreich bestanden waren, haben wir mit der Entwicklung des gesamten Industrialisierungsprozesses begonnen. In dieser Phase haben wir die Formen für die drei verschiedenen Ofenausführungen sowie Biege- und Schweißwerkzeuge erstellt. Nachdem wir die gesamte Konfiguration des Schweißprozesses vorbereitet hatten, widmeten wir uns der Optimierung des Reinigungsprozesses durch Abbeizen und lokale Passivierung. Das Ergebnis? Ein Produkt mit einer glatten Oberfläche, das Kontaminationen verhindert und mit einer zusätzlichen korrosionsbeständigen Schutzschicht ausgestattet ist.
Die Bedeutung von Zertifizierungen
Eine der grundlegenden Anforderungen dieses Projekts betrifft die Zertifizierungen. Im Hinblick auf das Schweißen verfügen wir bei Metal’s sowohl über die Zertifizierungen zur Qualität der Verarbeitung (EN ISO 3834-2:2021) als auch über die Zertifizierungen für die Schweißer (UNI EN ISO 9606-1:2017).
„Bei Projekten wie diesen, die spezifische und detaillierte Anforderungen haben, ist die Test- und Prototyping-Phase entscheidend, um festzustellen, ob man auf dem richtigen Weg ist. Es fordert Zeit, den Industrialisierungsprozess zu entwickeln, die Formen und Werkzeuge zu erstellen und die Bearbeitungen optimal zu konfigurieren, um die Fertigungszeiten zu verbessern und ein perfektes Produkt zu realisieren. Selbst wenn der Kunde klare Vorstellungen von den zu erreichenden Zielen hat, kann eine externe Meinung dazu beitragen, ein besseres Ergebnis zu erzielen. Ein langer Prozess in seinen ersten Phasen, der jedoch in jedem Aspekt verfeinert werden muss, um alle Anforderungen des Auftraggebers zu erfüllen und gleichzeitig auf Nachhaltigkeit zu achten.“ – Luca Regazzo, Technischer Vertriebsleiter
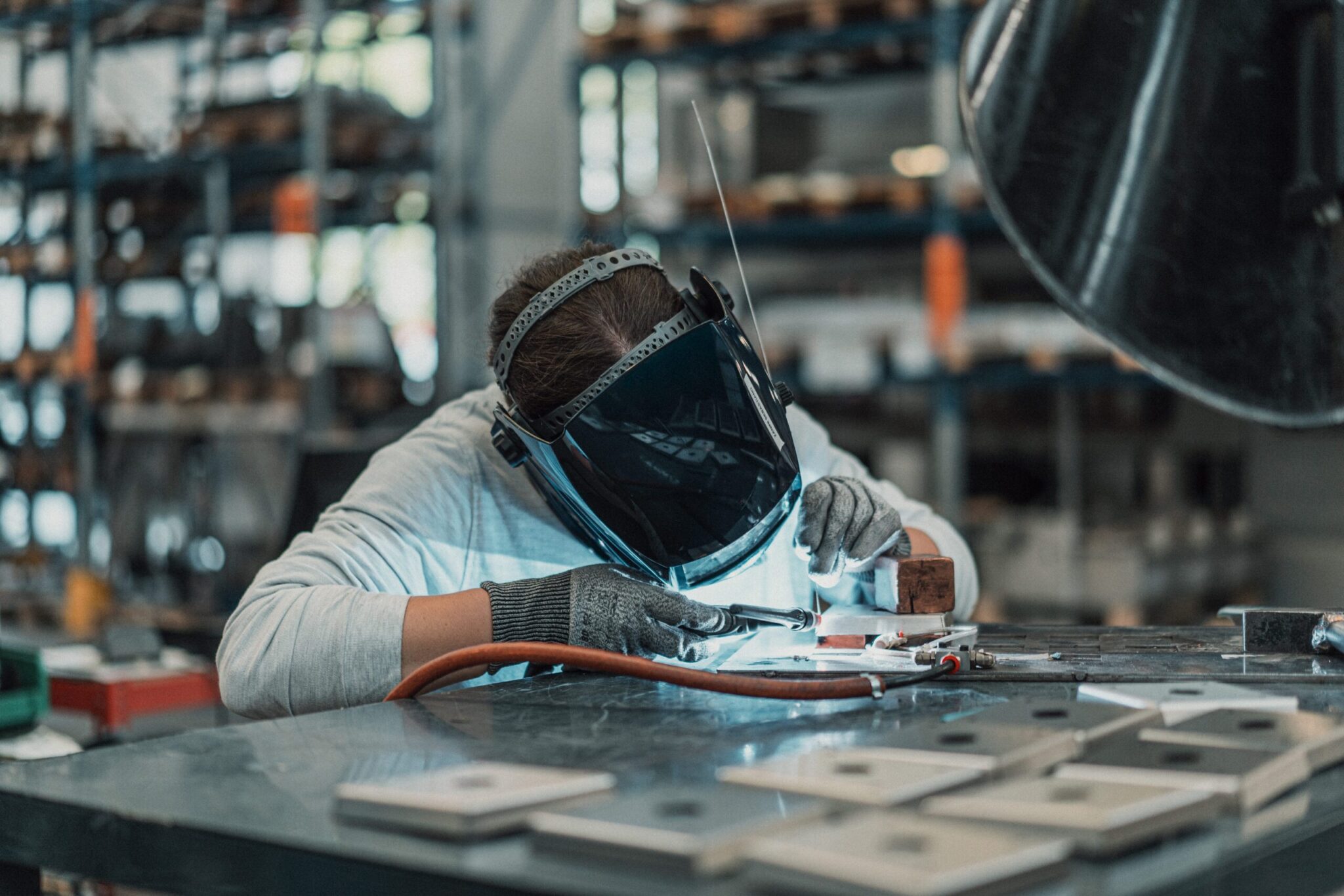
Lieferung, Lagerung und Logistik: ein grundlegender Baustein für einen effizienten und nachhaltigen Prozess
Bei Metal’s bieten wir einen umfassenden Service für die Supply-chain an, von der Beschaffung der Rohstoffe bis hin zum Versand des Produkts. Im Sinne einer nachhaltigen Verwaltung können unsere Kunden, die uns als einzigen Ansprechpartner wählen, auch auf die Organisation von Lieferungen, Lagerhaltung und Transport zählen.
Wir kontaktieren die Lieferanten, um die für die Produktion benötigten Materialien zu beschaffen, bereiten einen Sicherheitsbestand vor und organisieren mit dem Kunden die Fristen für den Versand der Ware, um die Lieferkette stets aktiv zu halten und möglichen Stillständen oder Notfällen entgegenzuwirken.
In diesem Sinne – und um die Produktion nicht zu überlasten – stellen wir die Halbfabrikate rechtzeitig her und montieren sie erst, wenn der im Vertrag vereinbarte Liefertermin näher rückt. Dies ermöglicht es uns, im Voraus zu arbeiten, unseren Kunden einen Lagerdienst anzubieten und die vereinbarten Fristen einzuhalten.
Wir bieten unsere Beratung an, um die richtige Verpackung zu finden, die verhindert, dass das Produkt während des Transports im Container oder auf dem Landweg beschädigt wird. Darüber hinaus planen wir den Versand und optimieren die Verladung (und die entsprechenden Kosten). In diesem Zusammenhang bevorzugen wir den Versand des Produkts mit voller Ladung und entwickeln effektive und nachhaltige Lösungen, um Kosten und Verschwendungen zu reduzieren und auch sichere Stapelung von Materialien zu berücksichtigen.
Schnelle Lösungen im Notfall
Was den Transport betrifft, muss man immer berücksichtigen, dass die Baugruppen und Halbfabrikate voluminös, aber sehr leicht sind.
Für den deutschen Kunden haben wir die Sendungen nach Europa und China vorbereitet, bei Entwicklung zwei verschiedenen Lösungen. Für Europa wurde ein Stapelungssystem von zwei Ofenmodellen innerhalb desselben LKW gewählt. Für die Lagerung in China hingegen hat unsere Konstruktion einen Anschluss entworfen, der am Produkt angebracht wird, um drei Stück anstelle von zwei im gleichen Raum versenden zu können.
Eine Option, die wir aufgrund unterschiedlicher Containermaße des Transporteurs kurzfristig neu planen mussten. Auch in einer Notsituation, kurz vor einer Sendung, haben wir uns schnell umorientiert, um die Verpackungseinheiten neu zu organisieren und den Auftrag dennoch fristgerecht abzuwickeln, wobei wir sicherstellten, dass die Ware gut verpackt und geschützt war. Eine Lösung, die es uns ermöglicht hat, die Anzahl der Sendungen zu reduzieren, Kosten zu reduzieren und die Umwelt weniger zu belasten.