Wenn unsere Verkaufsabteilung einen Auftrag für die Herstellung einer komplexen Baugruppe erhält, wird der Ablauf in Metal’s sofort gestartet, um Anforderungen und vereinbarten Zeitpläne unserer Kunden einzuhalten.
Wie funktioniert dieser Prozess? Welche Bereiche sind aktiv beteiligt, und welche Vorteile ergeben sich für diejenigen, die auf uns vertrauen?
Der Einkauf von Rohstoffen – insbesondere Edelstahl –, die Auftragsabwicklung, die Bestandsverwaltung, die Logistik und der Versand der Waren: die Koordination jeder Phase ist entscheidend. Die Inanspruchnahme der Dienstleistungen von Metal’s bedeutet, mit einem einzigen Partner zusammenzuarbeiten, der komplexe und spezialisierte Lieferketten vertikalisiert.
In diesem Artikel erläutern wir im Detail, wie wir die Rohstoffe beschaffen, wie wir sie vor der Produktion katalogisieren und welche Technologien im gesamten Prozess zum Einsatz kommen. So können wir die gemeinsam mit unseren Kunden entwickelten komplexen Baugruppen termingerecht liefern. Außerdem beleuchten wir die Rolle der Lieferkette und erklären, warum sie für das Unternehmen immer wichtiger wird.
Materialbeschaffung: Edelstahl
In einem früheren Artikel haben wir erläutert, wie wir bei Metal’s arbeiten und wie unser Produktionsprozess abläuft. In diesem Beitrag konzentrieren wir uns auf die Materialbeschaffung, die – in unserem Fall – vor allem den Einkauf von Edelstahl umfasst.
Die Hauptarten von Edelstahl, die wir in unserer Produktion verwenden, sind:
- AISI 304: Der Chromanteil (zwischen 18 und 20 %) und der Nickelanteil (zwischen 8 und 11 %) machen dieses Material hochwertig, äußerst korrosionsbeständig und leicht zu verarbeiten. Empfohlen für Produkte, die in der Lebensmittelkonservierung oder in der chemischen Industrie eingesetzt werden.
- AISI 430: Dieser ferritische Edelstahl ist besonders hitzebeständig.
- AISI 316: Ein Standard-Edelstahl mit variierenden Anteilen an Chrom (16–18 %), Nickel (11–14 %) und Molybdän (2–3 %). Dank seiner hohen Korrosionsbeständigkeit eignet er sich für die chemische, pharmazeutische und Lebensmittelindustrie.
Das Material wird von führenden europäischen Stahlwerken bezogen, die bereits zugeschnittene, flachgewalzte Bleche in spezifischen, standardisierten oder maßgeschneiderten Formaten liefern können. Selbstverständlich können wir auch andere Edelstahlsorten beschaffen, um die Anforderungen unserer Kunden bestmöglich zu erfüllen.
Präzise Bestellungen und sorgfältige Kontrolle bei Wareneingang
Sobald gemeinsam mit dem Kunden die am besten geeignete Edelstahlsorte für die Herstellung einer komplexen Baugruppe im fortgeschrittenen Montagezustand festgelegt wurde, geben wir die Bestellung in unser Verwaltungssystem ein und senden sie an den Lieferanten.
Die Bestellung wird mit Zeichnungen, allen technischen Spezifikationen und einem technischen Lieferprotokoll verschickt. Durch das detaillierte Protokoll geben wir dem Lieferanten sowohl technische (wie Maße und Stärke) als auch ästhetische (wie Oberfläche, Rauheit) Anforderungen an das Material vor. Auch die ausgewählte Verpackung wird hierin festgelegt, ein entscheidendes Detail, da all unsere Anlagen mit automatischen Ladesystemen ausgestattet sind und eine fehlerhafte Einschätzung den Produktionsprozess verlangsamen könnte.
Beim Wareneingang sollen die Lagerfachkräfte die Eignung der Ware und die Begleitdokumentation prüfen. Sie kontrollieren die Richtigkeit der Angaben und deren Übereinstimmung mit der Bestellung.
Zu jeder Lieferung gehört stets das Zertifikat 3.1 (gemäß der Norm EN 10204), welches die Herkunft der Schmelze des jeweiligen Materials angibt. Dieses Dokument enthält alle chemischen Eigenschaften des Edelstahls und ist sowohl für die Prüfung als auch für die Verarbeitung unerlässlich.
Wenn alles den Anforderungen entspricht, wird das Material gekennzeichnet und im Lager eingelagert, bereit für den Einsatz in der Produktion.
Die Bedeutung der Kennzeichnung
Die Kennzeichnung des Rohmaterials ist von zentraler Bedeutung, da die eindeutige Materialnummer sowohl das Los des Lieferanten als auch unser fertiges Produkt identifiziert. Auf diese Weise kann das Material jederzeit zurückverfolgt werden, selbst nach der Auslieferung der komplexen Baugruppe an unsere Kunden.
Dies stellt einen Mehrwert für die Kunden von Metal’s dar. Im Falle von Fehlermeldungen oder bei spezifischen Anforderungen wie der Rückverfolgbarkeit von Produkten, die beispielsweise für den medizinischen Sektor bestimmt sind, können wir jederzeit das Material ermitteln, das zur Herstellung eines jeden Artikels verwendet wurde.
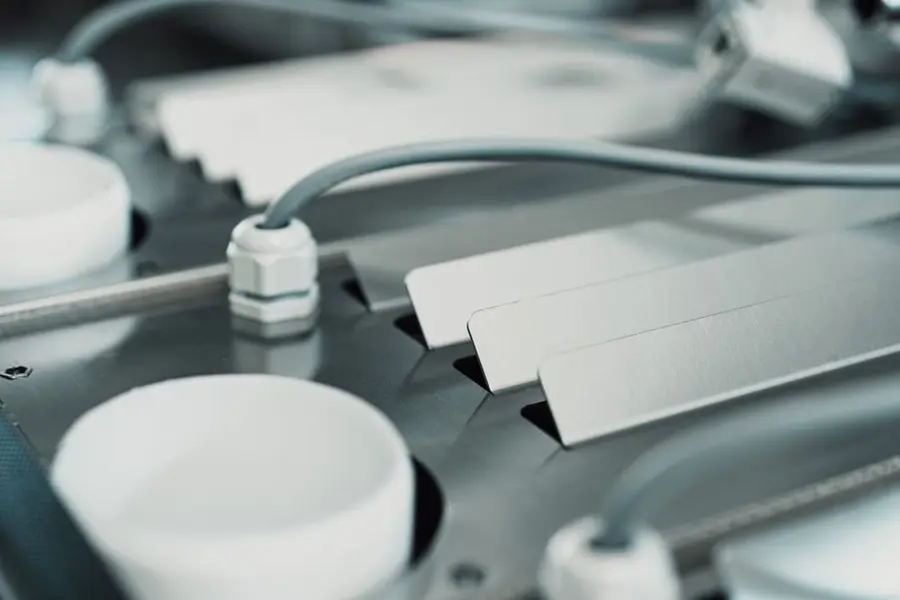
Mit einem fortschrittlichen Managementsystem ist jeder Prozess stets unter Kontrolle
Bei Metal’s setzen wir modernste Technologien für die Auftrags- und Produktionsflusssteuerung ein. Wie bereits erwähnt, erfolgt die Auftragsübermittlung an die Lieferanten mittels eines integriertes Managementsystems. Dieses Vorgehen beschleunigt die automatische Beschaffung von Materialien und ermöglicht die gemeinsame Nutzung wichtiger Dokumente wie Zeichnungen, Checklisten und Spezifikationen.
Unser ERP-System ist mit allen Bereichen von Metal’s verbunden – von der Verwaltung bis zum Lager – und liefert in Echtzeit eine präzise Übersicht über Bestände und Materialverbrauch für jedes spezifische Projekt. Dank einer fortschrittlichen Funktionalität, dem MRP-Algorithmus (Material Requirement Planning), analysiert das System die Bedarfe aus Verkaufsaufträgen und generiert entsprechende Bestell- oder Produktionsanforderungen.
Je nach Art des Artikels und den mit dem Kunden getroffenen Vereinbarungen werden Materialien automatisch vom System bestellt, um die Produktion nicht zu verzögern und potenzielle Materialengpässe zu vermeiden. Dabei werden alle Artikel durch unterschiedliche Beschaffungsrichtlinien verwaltet. Sicherheitsbestände, Produktionslose und Vorlaufzeiten werden manuell eingegeben, um die Einhaltung der vereinbarten Liefertermine sicherzustellen.
Um auf Marktanforderungen schnell zu reagieren, nutzen wir bei Metal’s zudem das Konsignationslager-System zur Bestandsverwaltung. Dabei wird – in Absprache mit unseren Lieferanten – eine bestimmte Menge Edelstahlbei uns gelagert, welche nur bei Bedarf verwendet wird. Der Vorteil? Stets Zugriff auf einen ausreichenden Rohstoffvorrat zu haben, für einen reibungslosen Arbeitsablauf.
Ein integriertes und gemeinsames System
Bei Metal’s haben wir uns für eine ERP-Software (Enterprise Resource Planning) entschieden, die das Produktionsparadigma Industry 4.0 erfüllt und stets mit unserem modernen Maschinenpark vernetzt ist.
Das ERP-System ist schon ürsprünglich in alle Bereiche wie MES (Manufacturing Execution System), WMS (Warehouse Management System) und TQM (Total Quality Management) integriert. So sind die Informationen zugänglich und einfach auf allen Unternehmensebenen in Echtzeit zu überwachen.
Im Detail:
- MES (Manufacturing Execution System) liefert die Fortschritte der Produktionsaufträge, erfasst die Zeiten in Echtzeit und teilt alle relevanten Dokumente.
- WMS (Warehouse Management System) ermöglicht eine präzise Verwaltung der Materialien, bestimmt die Platzierung der Artikel im Unternehmen und überwacht die Bestände.
- TQM (Total Quality Management) analysiert in Echtzeit etwaige Prozessabweichungen und stellt sicher, dass die festgelegten PPM- (Parts Per Million) Anforderungen des Marktes oder der internen Produktion erreicht werden.
Was passiert, wenn die Bestellung neben Edelstahl auch andere Materialien umfasst?
Für einige Kunden fertigen wir komplexe Baugruppen, welche die Montage von Edelstahl mit anderen Materialien erfordern. Für die Beschaffung der Rohstoffe können wir zwei Lösungsansätze verfolgen:
• Wir greifen auf unsere italienischen und internationalen Lieferanten zurück;
• Wir kontaktieren vertrauenswürdige Partner, die uns von unseren Kunden empfohlen werden.
Im ersten Fall können wir ein Angebot einholen und die benötigten Komponenten zu einem günstigen Preis und/oder unter besseren Lieferbedingungen beschaffen. Wenn die Bedingungen den Anforderungen unserer Kunden entsprechen, können wir mit der Bestellung fortfahren.
Auf Kundenwunsch können wir jederzeit eingreifen. Zum Beispiel während der Produktionsphase, um einen günstigeren Lieferanten zu suchen und so die Kosten zu optimieren, ohne die Produktqualität zu beeinträchtigen, oder im Notfall, wenn ein Bauteil ersetzt werden muss oder nicht mehr auf dem Markt verfügbar ist.
In einem schnellen und sich ständig wandelnden Markt stellt die Möglichkeit, auf einen einzigen Ansprechpartner für die Lieferung zurückzugreifen – der technisch versiert und in der Lage ist, sich an ständig wechselnde Anforderungen anzupassen – einen entscheidenden Wettbewerbsvorteil dar.
Eine Lösung auch für komplexe Baugruppen großen Umfangs
Wir haben unseren Standort um eine neue mechanische Abteilung für die Fertigung komplexer Baugruppen großen Umfangs erweitert. Ein automatisiertes System, ergänzt durch spezielle Anlagen wie Fräsmaschinen, ermöglicht es uns, auch bei kleinen Serien mit höchster Präzision zu arbeiten.
Dies bringt uns in die Lage, neue Herausforderungen anzunehmen -sowohl auf dem italienischen als auch auf dem internationalen Markt, von Europa bis Amerika. Wir können unseren Kunden ein immer umfassenderes Produkt anbieten – auch hinsichtlich ästhetischer Oberflächenbearbeitungen – und gleichzeitig die im Projekt vereinbarten Anforderungen erfüllen.
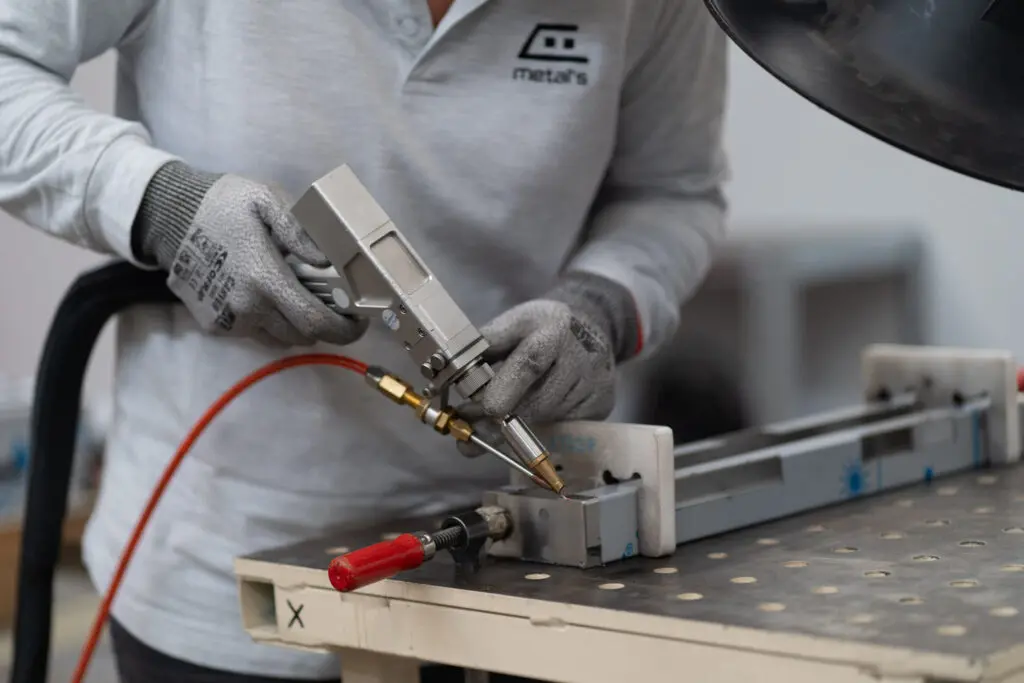
Auch das Management von Outsourcing-Aktivitäten ist digital
Wir haben ein SCC-Portal eingerichtet, um die Lieferkette für Outsourcing-Aktivitäten für Prozesse, welche die Unterstützung externer Lieferanten erfordern – wie z. B. Lackieren oder Elektropolieren – integriert zu verwalten. Auf diese Weise werden die vom ERP-System generierten Bestellungen direkt auf das Portal übertragen, das jederzeit für den Lieferanten zugänglich ist.
Ein benutzerfreundliches Werkzeug, das folgende Funktionen bietet:
• Erfassung von Bestellungen (einschließlich Zeichnungen und aller relevanten Informationen);
• Verfolgung des Produktionsfortschritts;
• Erstellung der notwendigen Aufkleber für Lieferung und Kennzeichnung der Ware.
So werden die Kommunikationswege auf ein Minimum reduziert, Informationsverluste vermieden und die Produktionszeiten optimiert.
Die Rolle der Supply Chain bei der Lieferung von Systemen im fortgeschrittenen Montagezustand
Eine durchdachte Verwaltung der unternehmenseigenen Supply Chain ermöglicht es uns, alle Phasen der Prozesskette – von der Beschaffung bis zur Distribution – zu koordinieren und zu optimieren.
Um sich in einem zunehmend wettbewerbsintensiven Markt zu behaupten, sind heute qualitativ hochwertige und termingerecht gelieferten Produkte erforderlich, wobei Wartezeiten, Abfall und Kosten reduziert sowie mögliche Produktionsunterbrechungen durch unvorhergesehene Ereignisse vermieden werden. Daher ist es entscheidend:
• die Beziehungen zu mehreren Partnern und Rohstofflieferanten effektiv zu koordinieren;
• vielfältige Bearbeitungen und umfassende Logistikpläne anzubieten, damit der Versand – vom Verpacken bis zur Lieferung – zufriedenstellend ist und die geltenden Vorschriften des Bestimmungsortes einhält.
Bei Metal’s können wir die gesamte Lieferkette verwalten und uns als einziger Ansprechpartner für Unternehmen positionieren, die einen umfassenden Service suchen – von der Rohstoffbeschaffung bis zur Lieferung der Aufträge – mit maßgeschneiderten Lösungen für unterschiedliche Industriebereiche. Dadurch können sich unsere Auftraggeber ganz auf ihre eigenen Tätigkeiten konzentrieren, während unsere Spezialisten die vollständige Koordination von Produktion und Logistik übernehmen.
Möchten Sie mehr erfahren?
Die Fertigung von komplexen Baugruppen aus Edelstahl umfasst den Kauf von Rohstoffen sowie deren Verarbeitung und Versand. Erfahren Sie, wie wir den gesamten Prozess ohne Verzögerungen abwickeln und welche Vorteile Sie genießen können, wenn Sie Metal’s als Ihren einzigen Ansprechpartner wählen.