Die Bearbeitung von Edelstahl ist nur ein Schritt in unserem Produktionsprozess. Bei Metal’s sind wir nämlich bestrebt, unseren Kunden einen kompletten Service zu bieten, der mit der Beratung beginnt und mit der Lieferung endet. Darüber haben wir bereits in dem Artikel über unsere Arbeitsweise gesprochen. Aber wie wird ein Projekt konkret entwickelt? Und wie gehen wir an einen Auftrag heran? Davon erzählen wir Ihnen in diesem Artikel, in dem wir einen realen Fall schildern.
Optimierung der Kosten, der Produktion und der Verarbeitung: ein Fallbeispiel von Metal‘s
Bei Metal’s wird jedes Projekt gemeinsam mit dem Kunden entwickelt, um die gesetzten Ziele zu erreichen und verschiedene Optionen zur Optimierung von Produktion, Kosten und Zeit vorzuschlagen.
Insbesondere in dem Fall, den wir in diesem Artikel darstellen, haben wir beschlossen, noch mehr über die Auswirkungen unserer Arbeit für die Unternehmen zu berichten, welche sich mit einer typischen Anfrage nach Kostenoptimierung auf uns verlassen.
Der Fall und die Anfrage in Kürze: Optimierung der Kosten ohne Abstriche bei Ästhetik, Funktionalität und Festigkeit
Ein wichtiger Kunde aus der Lebensmittelbranche beauftragte uns mit der Herstellung von Schranksystemen für Bäckereien, Einkaufszentren und Supermärkte. Das Ziel: Optimierung der Produktionskosten ohne Beeinträchtigung der Ästhetik des Produkts, seiner Funktionalität und Leistung, sowohl in Bezug auf die Steifigkeit als auch auf die Stabilität, zwei unabdingbare Eigenschaften, um die Bewegung der Schränke auf Rädern auch bei ungleichem Boden zu erleichtern.
Unser Vorschlag: fertig montierte Schranksysteme mit einer starken und leichten Struktur
In diesem Fall hatten wir vorgeschlagen, die Schranksysteme mit Hilfe spezieller Schneid- und Biegeverfahren herzustellen, die es uns ermöglichten, ein bereits montiertes Halbfertigprodukt aus Edelstahl zu erstellen. Das Produkt war fast identisch mit den zuvor für unseren Kunden gefertigten Schränken, mit einer starken und leichten Struktur und sofort einsatzbereit. Die Lösung, die wir gefunden haben, um dieses Ergebnis zu erreichen und die Kosten einzudämmen, beinhaltete auch die Studie eines Steckverbindungs- und Befestigungssystems, das unterschiedliche Stärken und Materialien berücksichtigte.
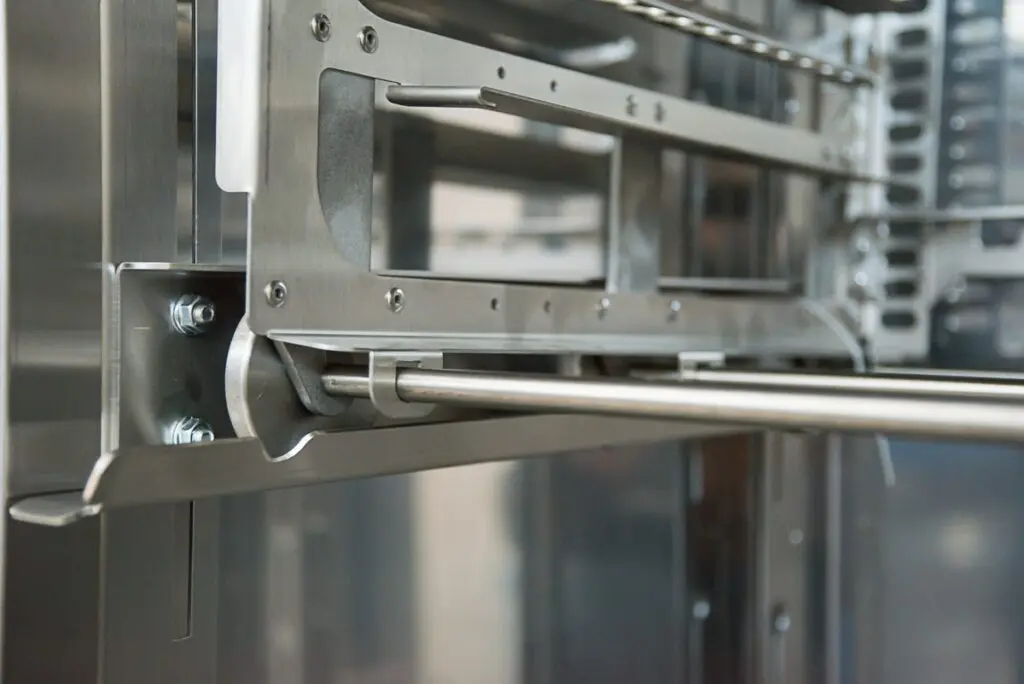
Die Bedeutung der Testphase: ein Prototyp, der vor Ort getestet wird
Unsere technische Abteilung untersuchte die möglichen Alternativen und schlug dem Kunden den Entwurf eines neuen Projektes vor, der passend zu seinen ursprünglichen Anforderungen war.Des Weiteren haben wir ein Muster angefertigt und geliefert, damit der Kunde die Kompatibilität mit den vereinbarten Anforderungen an Ästhetik, Funktionalität und Stabilität nachprüfen und das Muster durch verschiedene Belastungssimulationen unter realen Einsatzbedingungen testen konnte.
„Als sie uns fragten, ob es möglich sei, die Produktkosten zu senken und dabei die gleiche Ästhetik, Qualität und Funktionalität beizubehalten, setzten wir unsere technische Abteilung in Bewegung, um die beste Lösung für ihre Anfrage zu finden. Nachdem wir den ursprünglichen Entwurf des Kunden – bereits in der ersten Produktionsphase von uns optimiert – übernommen hatten, entwickelten wir ihn weiter. Dann haben wir einen Prototyp des Schranksystems erstellt, damit der Kunde es testen und die Vielseitigkeit und Steifigkeit des Produkts sowie das mögliche Vorhandensein von Verformungen und zu behebenden Mängeln überprüfen konnte“. – Luca Regazzo, Technischer Verkaufsleiter
Auf dem Weg zur Produktion: vom Prototyp zur Endprüfung
Nachdem wir die Tests bestanden und uns vergewissert hatten, dass der Prototyp den Anforderungen entsprach – in diesem Fall Vielseitigkeit, Robustheit, Ästhetik und Kostenreduzierung -, haben wir den eigentlichen Produktionszyklus gestartet und die Realisierung des Schranksystems, das anschließend auf den Zielmarkt gekommen ist.
Die Produktion ist eine Phase, in der wir noch sorgfältiger und strenger darauf achten, dass die Projektstandards – ohne die Lieferzeiten zu überschreiten – eingehalten werden. Dank unseres hochmodernen Maschinenparks, der jeden Tag 24 Stunden in Betrieb ist, können wir das Produkt termingerecht liefern.
„Jeder Arbeitsschritt des Schranksystems, einschließlich Produktion und Endbearbeitung, wurde von unseren technischen Experten überwacht, um die mit dem Kunden vereinbarten Ziele zu erreichen. Außerdem haben wir nach Fertigstellung des Produkts eine strenge Qualitätskontrolle durchgeführt, um die Tauglichkeit des Produkts zu prüfen.
Dies war möglich, weil wir das Projekt im Vorfeld entwickelt haben, um die nachfolgenden Schritte zu berücksichtigen. In der Tat arbeiten wir in Synergie – unter den Abteilungen von Metal‘s und mit dem Kunden – immer mit Ausgangspunkt eine Kundenzeichnung, die unsere technische Abteilung optimiert und entsprechend den Anforderungen des Kunden entwickelt. Die Realisierung mehrerer Renderings ermöglicht es dann, uns den gemeinsamen Zielen anzunähern, aber erst mit der Realisierung eines Prototyps können wir verstehen, ob es weitere Eingriffe erforderlich sind, um das Design zu verbessern. Nach der Prüfung des Musters kommt die Produktionsabteilung ins Spiel, wo jeder Schritt mit Präzision, Schnelligkeit und Pünktlichkeit ausgeführt wird. Auf diese Weise können wir die vereinbarten Termine einhalten und die geforderten hohen Standards erreichen, so dass wir unseren Kunden ein perfektes Produkt bieten können“. – Nicola Borella, Betriebsleiter
Ein einziger Partner für die komplexesten Projekte
Der in diesem Artikel geschilderte Fall ist nur eines von vielen Beispielen dafür, wie Metal’s tagtäglich sowohl als Lieferant als auch als echter Partner für Unternehmen in verschiedenen Branchen tätig ist. Finden Sie heraus, was wir für Sie tun können. Bei Ihren Produktionen verlassen Sie sich auf Metal’s.